Technologie de freinage
Créativité pour le freinage
12 février 2025 agvs-upsa.ch – Le frottement génère un couple de freinage au niveau de la roue, ce qui ralentit le véhicule. Ce qui constitue une physique éprouvée depuis des années connaît de nouveaux champs de réflexion en raison des prochaines valeurs limites d’émission Euro 7, qui limitent également l’abrasion des freins. Des innovations ingénieuses assurent la créativité dans la mise en oeuvre. Andreas Senger
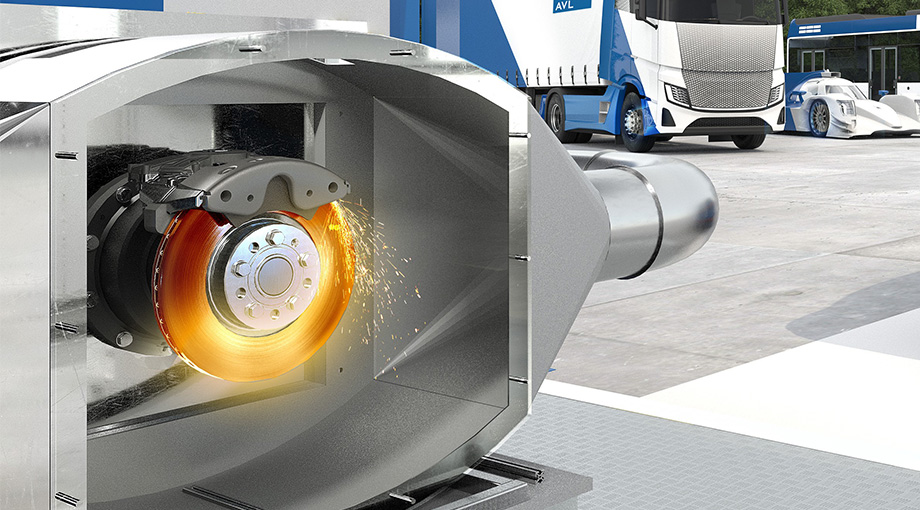
Pour tester l’abrasion d’un frein à disque en cours de développement, la poussière de frein est aspirée et analysée sur un banc d’essai fermé. Photo : AVL
Un disque de freinage ou un tambour de frein fonctionnent selon le même principe physique : le frottement entre la garniture de frein et le métal transforme l’énergie cinétique en énergie thermique. Le couple de freinage généré sur la roue est transformé par le rayon efficace du pneu en une force de freinage entre le pneu et la chaussée, qui agit dans le sens inverse de la marche. Grâce à la répartition électronique de la force de freinage, le freinage en ligne droite est aujourd’hui à l’ordre du jour.

Sur le prototype de frein In-Drive présenté, la garniture defrein (main gauche) tourne et le disque de freinage refroidipar liquide de refroidissement (à gauche avec denture extérieure) est immobile. Le disque de freinage 360° est relié à la bride de l’arbre d’entraînement par une denture intérieure. L’actionnement n’est pas encore montré par Mercedes. Photo : Mercedes-Benz
Ce processus de freinage a été révolutionné par la transmission électrique. Une machine électrique peut non seulement assurer la propulsion, mais aussi la décélération grâce à la récupération d’énergie. En convertissant l’énergie cinétique en énergie électrique, on obtient également un couple de freinage sur la roue avec conversion en force de freinage par le biais du rayon effectif du pneu. La décélération maximale est toutefois limitée si l’énergie cinétique transformée en énergie électrique par induction doit également pouvoir être absorbée par la batterie. Bien que plus de 1000 ampères circulent brièvement dans les câbles de la puissante transmission électrique, la batterie haute tension empêche les phases de récupération prolongées. En raison de la résistance interne, les cellules s’échauffent fortement lorsqu’elles absorbent le courant (résistance interne des cellules). La seule solution serait d’utiliser des résistances à haut rendement (comme dans les trains de montagne historiques) qui transforment le courant de récupération en chaleur.
Pour les freinages de longue durée, comme dans les descentes de cols ou en cas de décélération plus importante (au-dessus du freinage par récupération), il faudra continuer à installer un système de freinage à friction. Mercedes-Benz fait valoir qu’il est actuellement possible d’obtenir une puissance de freinage d’environ 0,3 MW en cas de récupération, mais que 2,2 MW sont nécessaires pour un freinage d’urgence. La future norme Euro 7 limitera les émissions de pneus et de poussières de frein. En conséquence, de nouvelles pistes de réflexion sont explorées afin de garantir le freinage minimal prescrit par la loi et, d’autre part, de réduire le nombre et la masse des particules de freinage.
Optimiser le couple de matériaux
La plaquette de frein a une grande influence sur le comportement de freinage, la durée de vie et les émissions de poussières de frein. Différents composants (voir AUTOINSIDE 12/24 pages 34 à 37) assurent un coefficient de friction élevé entre la garniture (fixe) et le disque de freinage ou le tambour (rotatif). Le fait que les défis techniques de la dissipation de la chaleur, du fading (diminution du coefficient de frottement à haute température) et, en même temps, d’une durée de vie aussi longue que possible puissent être résolus aujourd’hui dans la recherche et le développement grâce à des ingrédients appropriés, est un côté de la médaille. Désormais, les émissions de poussières de frein doivent également être considérablement réduites. Différents concepts, en plus d’un choix optimal des matériaux, assurent des développements innovants.

Le nouveau système de freinage est directement bridé à gauche et à droite de la machine électrique. Photo : Mercedes-Benz
Frein à tambour pour les personnes soucieuses de leur budget
Si la poussière de frein reste à l’intérieur du système de freinage, aucune émission n’est transférée dans l’environnement. Le frein à tambour est depuis toujours le garant de la mise en oeuvre de ce principe dans la grande majorité des cas. Pour les véhicules des segments des petites et moyennes cylindrées, cela constituera un moyen valable de garantir le freinage minimum légal tout en respectant les limites d’émission Euro 7. Toutefois, les freins à tambour ne peuvent être utilisés que sous certaines conditions sur l’essieu avant en raison de la dissipation de chaleur plus faible. Si le véhicule est lourd, le frein à tambour atteint ses limites à cause du fading. En raison d’une mauvaise évacuation de la chaleur, les plaquettes de frein s’échauffent tellement que le coefficient de frottement diminue et que l’effet de freinage s’affaiblit. Un autre inconvénient est la masse non suspendue relativement élevée des freins à tambour et à disque actuels. Plus un véhicule est lourd, plus la puissance de freinage doit être importante et les composants de freinage doivent être dimensionnés en conséquence. Sur les véhicules coûteux, on utilise des disques de freinage en carbone-céramique correspondants. Pour les véhicules moins chers, ces ralentisseurs au coût exorbitant sont économiquement irréalisables. Pour les deux disques et tambours conventionnels, des variantes innovantes de construction légère sont mises en oeuvre, dans lesquelles seule la bague de friction est en fonte ou en acier noble. Le support de disque de frein ou le tambour sont fabriqués en alliage léger ou en acier. Ces disques et tambours composites sont plus légers. Le thème de la poussière de frein peut être amélioré par une application de surface au moyen d’un procédé de soudage au laser et des garnitures de friction correspondantes. Ces options existent en grande partie sur le marché et seront développées et optimisées à l’avenir.
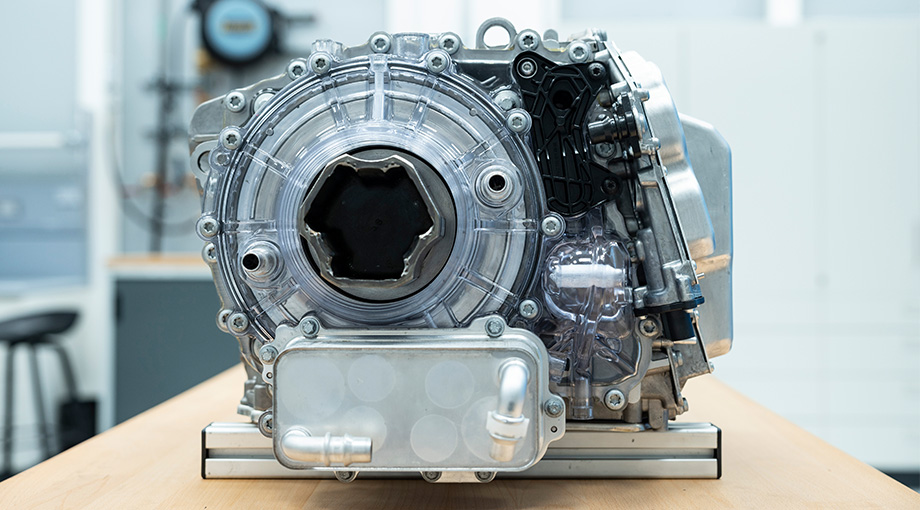
Les deux raccords de liquide de refroidissement assurent la dissipation de la chaleur au niveau du disque de freinage. Photo : Mercedes-Benz
Pour maintenir la masse non suspendue à un faible niveau, les disques de freinage intérieurs existaient dans le passé. Des constructeurs tels qu’Alfa Romeo, Audi, DKW, Citroën, NSU ou Jaguar ont certes réduit la masse non suspendue, mais en transmettant le couple de freinage à la roue via l’arbre de transmission, ils ont entraîné une usure plus importante des articulations. Néanmoins, Mercedes-Benz a repris cette idée dans une nouvelle interprétation et l’a nettement modifiée. Le frein In-Drive, qui sera présenté fin 2024, reprend l’idée de la réduction de la masse sur les roues. Le frein à friction est monté à gauche et à droite directement sur la machine électrique et donc sur l’équilibrage du différentiel. Une idée extrêmement innovante est le système de refroidissement, qui posait souvent problème sur les équivalents historiques. Avec le frein In-Drive, ce n’est pas le disque de freinage qui tourne et qui est freiné par la garniture de frein fixe, mais la garniture de frein qui tourne et le disque de freinage qui s’arrête. En conséquence, il est possible d’évacuer la chaleur de frottement du disque de freinage via le liquide de refroidissement (deux raccords vers l’extérieur pour chaque) et d’éviter l’évanouissement des freins. La garniture de frein n’est pas fabriquée sous la forme d’un segment de cercle, mais d’un disque complet, relié à la bride d’entraînement par une denture. Cette bride d’entraînement est reliée d’un côté au différentiel et de l’autre, le joint tripode de l’arbre d’entraînement est enfiché. Grâce à un actionnement du prototype qui n’a pas encore été montré, une bague de friction fixe est maintenant poussée latéralement de l’intérieur contre la garniture de frein rotative, qui peut à son tour se déplacer également latéralement contre le disque de freinage extérieur. Il en résulte un frottement qui transforme l’énergie cinétique en chaleur. Pour refroidir le disque de friction intérieur, la chaleur sera probablement refroidie par de l’huile et l’actionnement se fera logiquement au moyen d’une commande hydraulique.
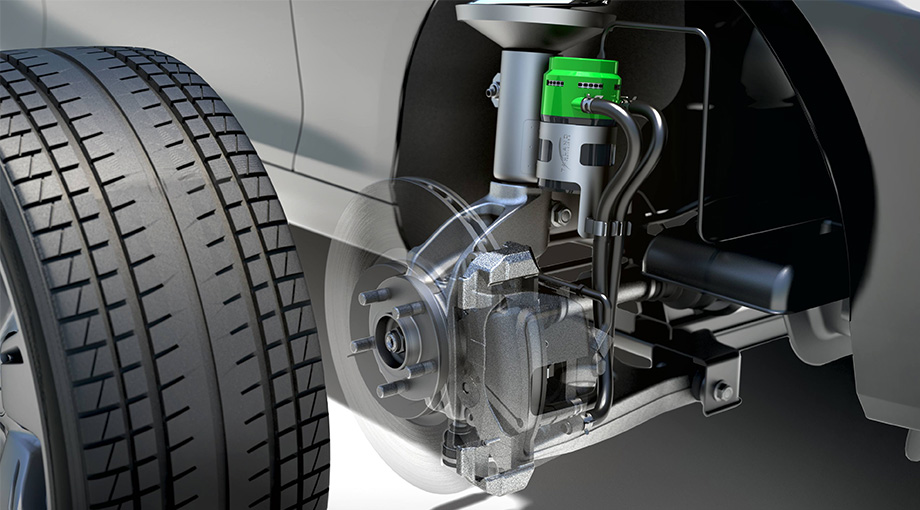
L’industrie des fournisseurs bricole des dispositifs d’aspiration ou des systèmes de filtrage passifs pour aspirer (activement) ou absorber (passivement) la poussière de frein des variantes de disques de frein pendant le processus de décélération. Photo : Tallano
Pour Mercedes-Benz, le déplacement du frein de roue vers la machine électrique présente non seulement l’avantage de réduire la masse non suspendue d’environ 40 %, mais aussi un avantage aérodynamique. Comme le disque ne doit plus être refroidi par une arrivée d’air comme dans les constructions conventionnelles et que l’arrivée d’air doit donc se faire sous le véhicule vers le frein de roue comme à travers les roues, il est possible d’utiliser des disques de roue fermés. Le Design des roues optimisé en termes de résistance à l’air permet de réduire la consommation d’énergie grâce à l’absence de turbulences d’air.
Par ailleurs, le constructeur automobile vise avec le frein In-Drive une application à vie et donc une durée de stockage de l’installation de plus de 300 000 kilomètres. Grâce à la garniture de friction en arc de cercle, cela semble réaliste, car le frein n’est actionné que lorsque les exigences de décélération sont élevées. En règle générale, le freinage s’effectue par récupération. Le fabricant a également résolu le problème de la poussière de frein de manière intelligente : le boîtier fermé empêche l’émission de poussière, qui peut être collectée dans le bac de récupération situé dans la partie inférieure du boîtier et vidée à l’occasion des travaux d’entretien.
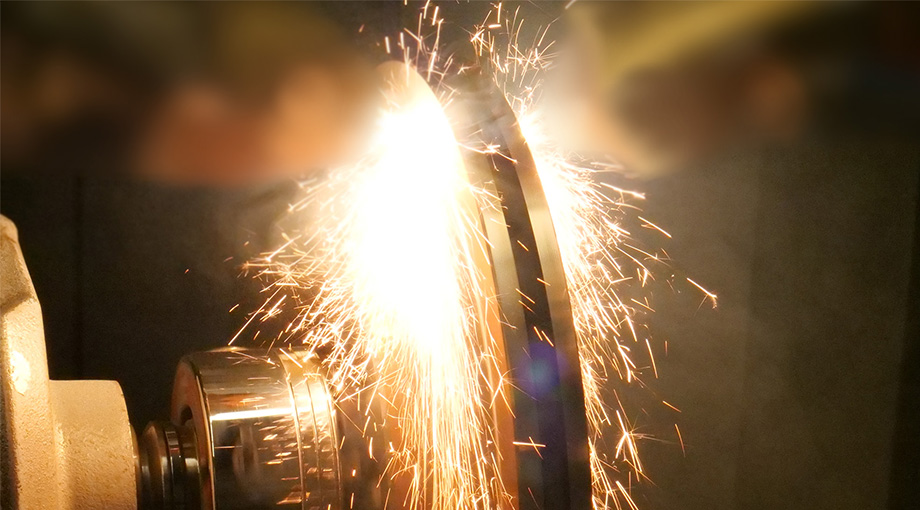
Des variantes de métal appliquées par laser permettent d’optimiser les éléments de friction. Photo : Laserline
Si un fabricant de freins ne peut pas optimiser ses éléments de friction en termes de matériaux pour respecter les limites d’émission de la norme Euro 7, des filtres à poussière de frein passifs ou actifs peuvent également être utilisés. Dans les systèmes passifs, une enveloppe filtrante est montée autour du disque de freinage et remplacée à l’occasion de l’entretien. Dans les systèmes actifs, la poussière de frein produite est aspirée à chaque freinage dans un récipient filtrant au moyen d’un dispositif d’aspiration. Ces deux concepts sont certes techniquement réalisables, mais moins intéressants en termes de coûts, tant pour les constructeurs automobiles que pour la clientèle, car ils impliquent des frais d’entretien élevés. La recherche et le développement visant à réduire les poussières de freinage par le biais de couples de frottement innovants semblent plus pertinents. Le législateur oblige les constructeurs automobiles à innover dans le domaine du freinage et donc à réduire les émissions de particules dues au trafic routier. La technique propose des solutions et fait avancer le développement et la recherche dans le domaine du freinage.
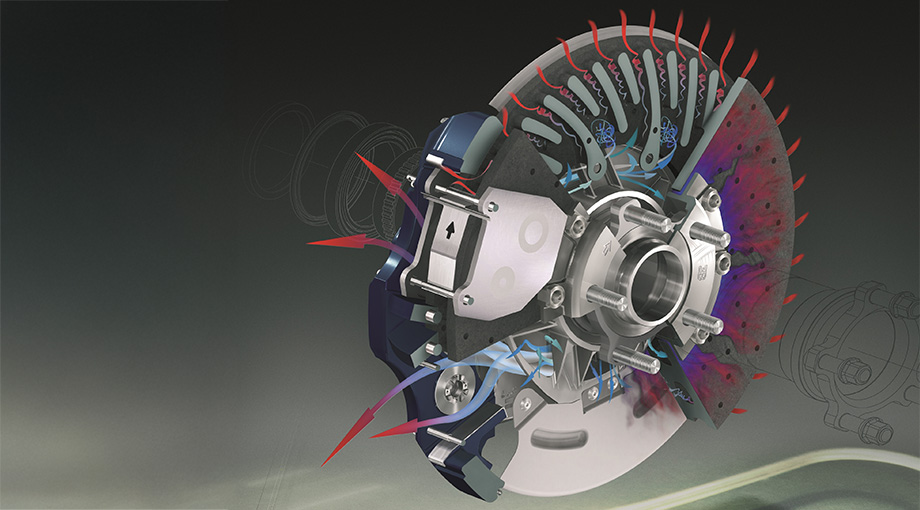
La dissipation de la chaleur des freins à disque par rapport aux freins à tambour est plus optimale. Photo : Bugatti
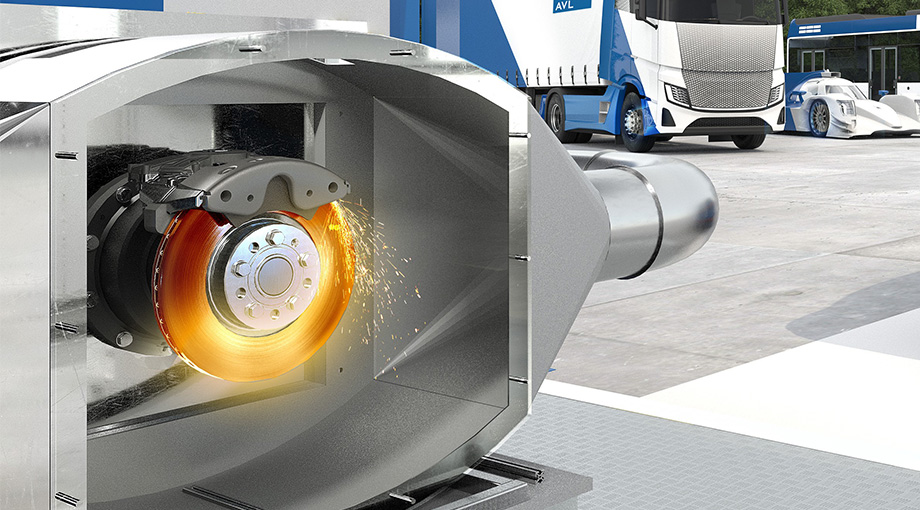
Pour tester l’abrasion d’un frein à disque en cours de développement, la poussière de frein est aspirée et analysée sur un banc d’essai fermé. Photo : AVL
Un disque de freinage ou un tambour de frein fonctionnent selon le même principe physique : le frottement entre la garniture de frein et le métal transforme l’énergie cinétique en énergie thermique. Le couple de freinage généré sur la roue est transformé par le rayon efficace du pneu en une force de freinage entre le pneu et la chaussée, qui agit dans le sens inverse de la marche. Grâce à la répartition électronique de la force de freinage, le freinage en ligne droite est aujourd’hui à l’ordre du jour.

Sur le prototype de frein In-Drive présenté, la garniture defrein (main gauche) tourne et le disque de freinage refroidipar liquide de refroidissement (à gauche avec denture extérieure) est immobile. Le disque de freinage 360° est relié à la bride de l’arbre d’entraînement par une denture intérieure. L’actionnement n’est pas encore montré par Mercedes. Photo : Mercedes-Benz
Ce processus de freinage a été révolutionné par la transmission électrique. Une machine électrique peut non seulement assurer la propulsion, mais aussi la décélération grâce à la récupération d’énergie. En convertissant l’énergie cinétique en énergie électrique, on obtient également un couple de freinage sur la roue avec conversion en force de freinage par le biais du rayon effectif du pneu. La décélération maximale est toutefois limitée si l’énergie cinétique transformée en énergie électrique par induction doit également pouvoir être absorbée par la batterie. Bien que plus de 1000 ampères circulent brièvement dans les câbles de la puissante transmission électrique, la batterie haute tension empêche les phases de récupération prolongées. En raison de la résistance interne, les cellules s’échauffent fortement lorsqu’elles absorbent le courant (résistance interne des cellules). La seule solution serait d’utiliser des résistances à haut rendement (comme dans les trains de montagne historiques) qui transforment le courant de récupération en chaleur.
Pour les freinages de longue durée, comme dans les descentes de cols ou en cas de décélération plus importante (au-dessus du freinage par récupération), il faudra continuer à installer un système de freinage à friction. Mercedes-Benz fait valoir qu’il est actuellement possible d’obtenir une puissance de freinage d’environ 0,3 MW en cas de récupération, mais que 2,2 MW sont nécessaires pour un freinage d’urgence. La future norme Euro 7 limitera les émissions de pneus et de poussières de frein. En conséquence, de nouvelles pistes de réflexion sont explorées afin de garantir le freinage minimal prescrit par la loi et, d’autre part, de réduire le nombre et la masse des particules de freinage.
Optimiser le couple de matériaux
La plaquette de frein a une grande influence sur le comportement de freinage, la durée de vie et les émissions de poussières de frein. Différents composants (voir AUTOINSIDE 12/24 pages 34 à 37) assurent un coefficient de friction élevé entre la garniture (fixe) et le disque de freinage ou le tambour (rotatif). Le fait que les défis techniques de la dissipation de la chaleur, du fading (diminution du coefficient de frottement à haute température) et, en même temps, d’une durée de vie aussi longue que possible puissent être résolus aujourd’hui dans la recherche et le développement grâce à des ingrédients appropriés, est un côté de la médaille. Désormais, les émissions de poussières de frein doivent également être considérablement réduites. Différents concepts, en plus d’un choix optimal des matériaux, assurent des développements innovants.

Le nouveau système de freinage est directement bridé à gauche et à droite de la machine électrique. Photo : Mercedes-Benz
Frein à tambour pour les personnes soucieuses de leur budget
Si la poussière de frein reste à l’intérieur du système de freinage, aucune émission n’est transférée dans l’environnement. Le frein à tambour est depuis toujours le garant de la mise en oeuvre de ce principe dans la grande majorité des cas. Pour les véhicules des segments des petites et moyennes cylindrées, cela constituera un moyen valable de garantir le freinage minimum légal tout en respectant les limites d’émission Euro 7. Toutefois, les freins à tambour ne peuvent être utilisés que sous certaines conditions sur l’essieu avant en raison de la dissipation de chaleur plus faible. Si le véhicule est lourd, le frein à tambour atteint ses limites à cause du fading. En raison d’une mauvaise évacuation de la chaleur, les plaquettes de frein s’échauffent tellement que le coefficient de frottement diminue et que l’effet de freinage s’affaiblit. Un autre inconvénient est la masse non suspendue relativement élevée des freins à tambour et à disque actuels. Plus un véhicule est lourd, plus la puissance de freinage doit être importante et les composants de freinage doivent être dimensionnés en conséquence. Sur les véhicules coûteux, on utilise des disques de freinage en carbone-céramique correspondants. Pour les véhicules moins chers, ces ralentisseurs au coût exorbitant sont économiquement irréalisables. Pour les deux disques et tambours conventionnels, des variantes innovantes de construction légère sont mises en oeuvre, dans lesquelles seule la bague de friction est en fonte ou en acier noble. Le support de disque de frein ou le tambour sont fabriqués en alliage léger ou en acier. Ces disques et tambours composites sont plus légers. Le thème de la poussière de frein peut être amélioré par une application de surface au moyen d’un procédé de soudage au laser et des garnitures de friction correspondantes. Ces options existent en grande partie sur le marché et seront développées et optimisées à l’avenir.
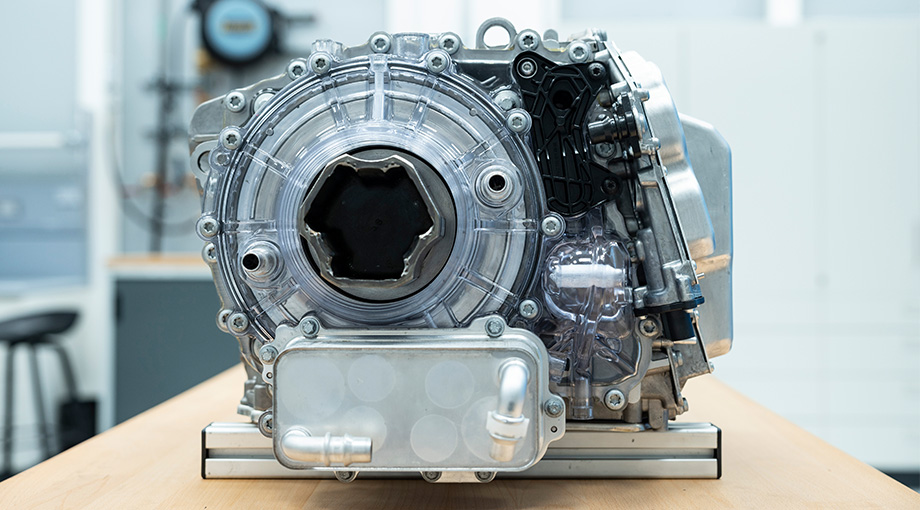
Les deux raccords de liquide de refroidissement assurent la dissipation de la chaleur au niveau du disque de freinage. Photo : Mercedes-Benz
Pour maintenir la masse non suspendue à un faible niveau, les disques de freinage intérieurs existaient dans le passé. Des constructeurs tels qu’Alfa Romeo, Audi, DKW, Citroën, NSU ou Jaguar ont certes réduit la masse non suspendue, mais en transmettant le couple de freinage à la roue via l’arbre de transmission, ils ont entraîné une usure plus importante des articulations. Néanmoins, Mercedes-Benz a repris cette idée dans une nouvelle interprétation et l’a nettement modifiée. Le frein In-Drive, qui sera présenté fin 2024, reprend l’idée de la réduction de la masse sur les roues. Le frein à friction est monté à gauche et à droite directement sur la machine électrique et donc sur l’équilibrage du différentiel. Une idée extrêmement innovante est le système de refroidissement, qui posait souvent problème sur les équivalents historiques. Avec le frein In-Drive, ce n’est pas le disque de freinage qui tourne et qui est freiné par la garniture de frein fixe, mais la garniture de frein qui tourne et le disque de freinage qui s’arrête. En conséquence, il est possible d’évacuer la chaleur de frottement du disque de freinage via le liquide de refroidissement (deux raccords vers l’extérieur pour chaque) et d’éviter l’évanouissement des freins. La garniture de frein n’est pas fabriquée sous la forme d’un segment de cercle, mais d’un disque complet, relié à la bride d’entraînement par une denture. Cette bride d’entraînement est reliée d’un côté au différentiel et de l’autre, le joint tripode de l’arbre d’entraînement est enfiché. Grâce à un actionnement du prototype qui n’a pas encore été montré, une bague de friction fixe est maintenant poussée latéralement de l’intérieur contre la garniture de frein rotative, qui peut à son tour se déplacer également latéralement contre le disque de freinage extérieur. Il en résulte un frottement qui transforme l’énergie cinétique en chaleur. Pour refroidir le disque de friction intérieur, la chaleur sera probablement refroidie par de l’huile et l’actionnement se fera logiquement au moyen d’une commande hydraulique.
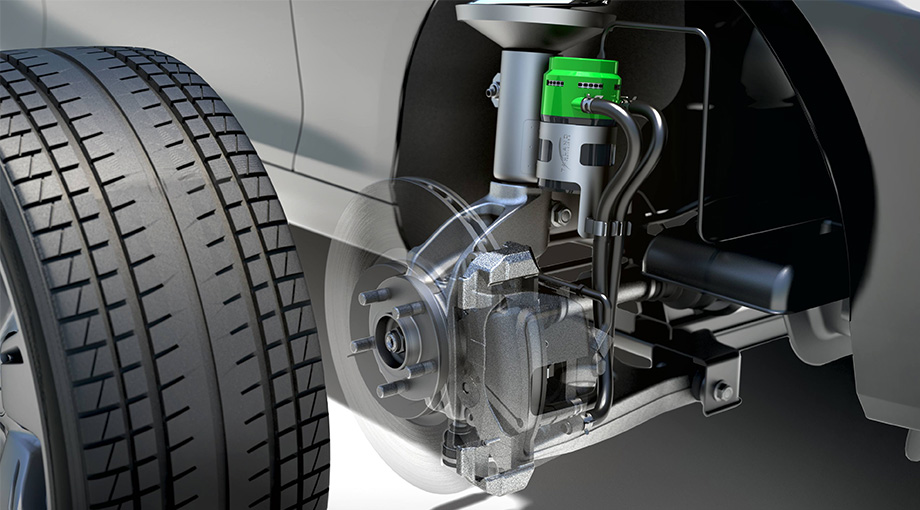
L’industrie des fournisseurs bricole des dispositifs d’aspiration ou des systèmes de filtrage passifs pour aspirer (activement) ou absorber (passivement) la poussière de frein des variantes de disques de frein pendant le processus de décélération. Photo : Tallano
Pour Mercedes-Benz, le déplacement du frein de roue vers la machine électrique présente non seulement l’avantage de réduire la masse non suspendue d’environ 40 %, mais aussi un avantage aérodynamique. Comme le disque ne doit plus être refroidi par une arrivée d’air comme dans les constructions conventionnelles et que l’arrivée d’air doit donc se faire sous le véhicule vers le frein de roue comme à travers les roues, il est possible d’utiliser des disques de roue fermés. Le Design des roues optimisé en termes de résistance à l’air permet de réduire la consommation d’énergie grâce à l’absence de turbulences d’air.
Par ailleurs, le constructeur automobile vise avec le frein In-Drive une application à vie et donc une durée de stockage de l’installation de plus de 300 000 kilomètres. Grâce à la garniture de friction en arc de cercle, cela semble réaliste, car le frein n’est actionné que lorsque les exigences de décélération sont élevées. En règle générale, le freinage s’effectue par récupération. Le fabricant a également résolu le problème de la poussière de frein de manière intelligente : le boîtier fermé empêche l’émission de poussière, qui peut être collectée dans le bac de récupération situé dans la partie inférieure du boîtier et vidée à l’occasion des travaux d’entretien.
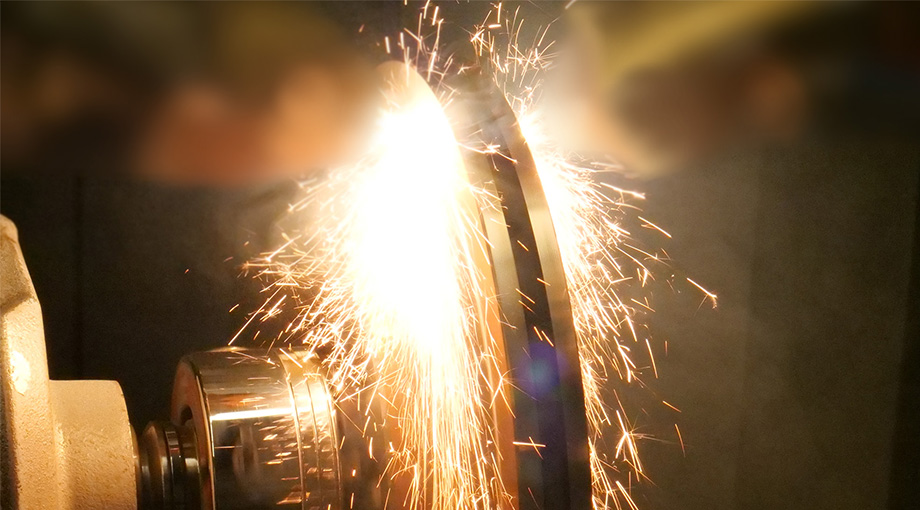
Des variantes de métal appliquées par laser permettent d’optimiser les éléments de friction. Photo : Laserline
Si un fabricant de freins ne peut pas optimiser ses éléments de friction en termes de matériaux pour respecter les limites d’émission de la norme Euro 7, des filtres à poussière de frein passifs ou actifs peuvent également être utilisés. Dans les systèmes passifs, une enveloppe filtrante est montée autour du disque de freinage et remplacée à l’occasion de l’entretien. Dans les systèmes actifs, la poussière de frein produite est aspirée à chaque freinage dans un récipient filtrant au moyen d’un dispositif d’aspiration. Ces deux concepts sont certes techniquement réalisables, mais moins intéressants en termes de coûts, tant pour les constructeurs automobiles que pour la clientèle, car ils impliquent des frais d’entretien élevés. La recherche et le développement visant à réduire les poussières de freinage par le biais de couples de frottement innovants semblent plus pertinents. Le législateur oblige les constructeurs automobiles à innover dans le domaine du freinage et donc à réduire les émissions de particules dues au trafic routier. La technique propose des solutions et fait avancer le développement et la recherche dans le domaine du freinage.
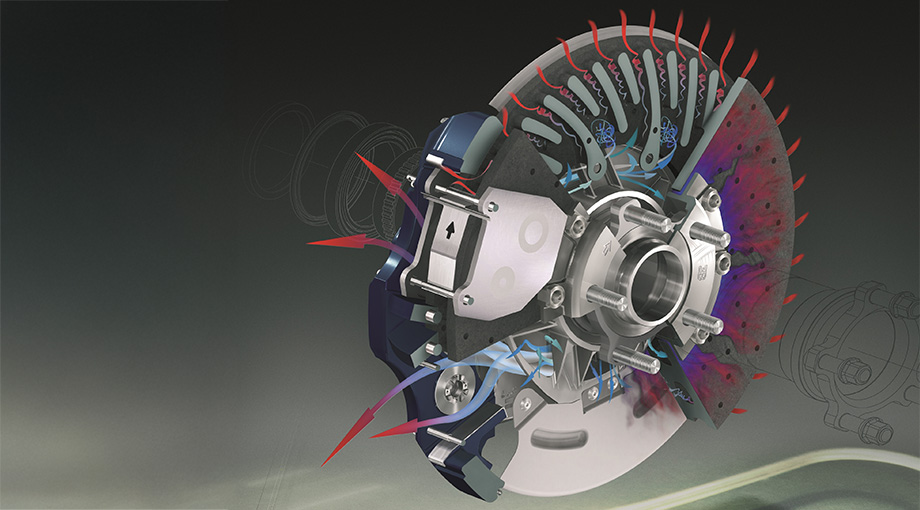
La dissipation de la chaleur des freins à disque par rapport aux freins à tambour est plus optimale. Photo : Bugatti
Ajouter un commentaire
Commentaires